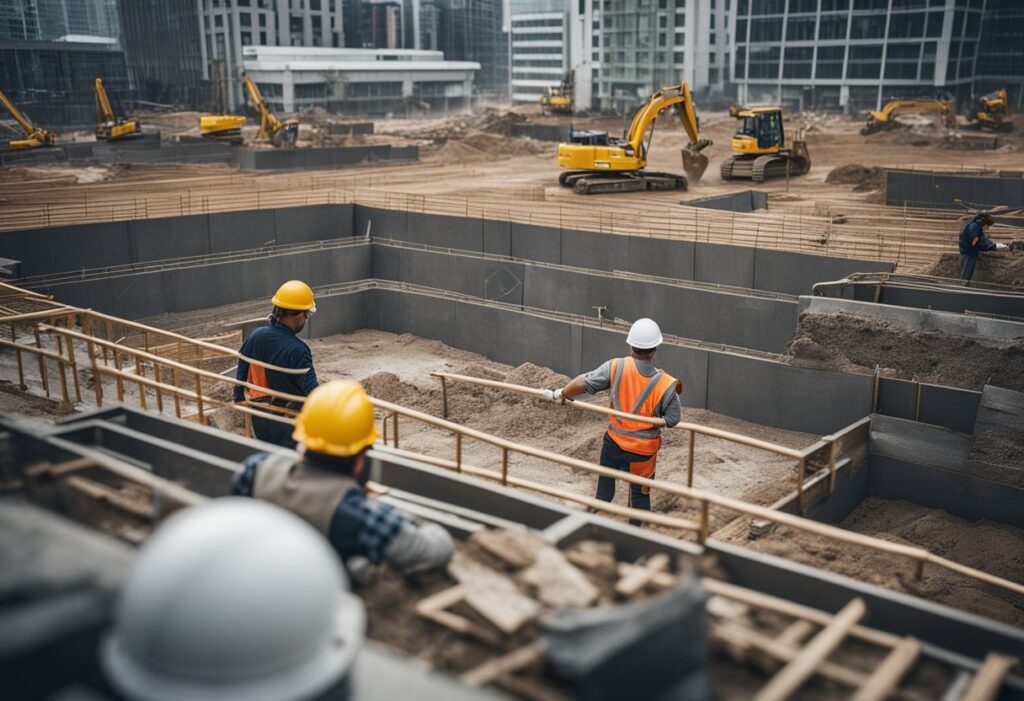
Construction delays can significantly impact project timelines and budgets. The most common reasons for these delays include weather conditions, supply chain disruptions, and insufficient planning. Understanding these factors can help stakeholders anticipate challenges and develop effective strategies to mitigate risks.
Weather-related issues often catch construction teams off guard, leading to project stalls. Additionally, unanticipated supply shortages can slow progress, causing frustration among contractors and clients alike. It is crucial for those involved in construction to recognize these potential setbacks early in the planning process.
Another frequent cause of delays stems from inadequate project management. Poor communication and lack of coordination among teams can create confusion, further hindering progress. By addressing these common issues, teams can enhance efficiency and keep projects on track.
Planning and Pre-Construction Challenges
Construction projects often encounter significant delays during the planning and pre-construction phases. Two key factors contributing to these delays are permit and approval processes, as well as project design changes.
Permit and Approval Delays
Delays associated with permits and approvals can significantly impact the overall timeline of a construction project. Obtaining the necessary permits requires compliance with local, state, and federal regulations, which can be complex. Delays may occur due to:
- Incomplete Applications: Errors or missing information in applications can result in resubmissions.
- Bureaucratic Processes: Slow approval processes in government offices can stall projects.
- Public Disclosures: Required public hearings or notifications can extend approval timelines.
Residential contractors often find themselves navigating intricate systems of zoning laws and environmental regulations, adding further complexity to the permitting process.
Project Design Changes
Project design changes can emerge for various reasons, often leading to delays in construction. Such changes may arise from:
- Client Requests: Modifications based on client preferences or budget revisions can necessitate redesigns.
- Regulatory Compliance: Changes in regulations require adaptations to original designs.
- Site Conditions: Unexpected issues, like soil quality or existing structures, can lead to redesigns.
Adjustments in project design not only require additional time but may also necessitate new permits, further complicating the timeline. A residential contractor must communicate effectively with stakeholders to minimize the impact of design changes on project schedules.
Operational and Executional Hurdles
Construction projects often face operational and executional hurdles that can lead to significant delays. These challenges can arise from various aspects of the project, impacting timelines and budgets.
Supply Chain Interruptions
Supply chain interruptions can occur due to multiple factors, including natural disasters, geopolitical issues, or market fluctuations. When materials or components are delayed, it directly affects the schedule. For instance, an unanticipated shortage of concrete or lumber can stall critical phases of construction.
Additionally, vendor reliability plays a crucial role. If a contractor depends on suppliers who consistently fail to meet deadlines, this can compound delays. Establishing strong relationships with multiple suppliers can be an effective strategy to mitigate risks associated with supply shortages.
Workforce Management Issues
Workforce management issues can severely hinder a construction project’s progress. Labor shortages, especially in specialized trades, create bottlenecks. When there are not enough skilled workers available, projects cannot proceed as planned.
Moreover, miscommunication among team members can lead to errors or inefficiencies. Workers must have clear directives and sufficient training to avoid costly mistakes that require rework. Implementing robust management systems can help streamline operations and enhance productivity on-site.
Equipment and Technology Failures
Equipment and technology failures can cause unexpected project setbacks. Malfunctioning machinery, such as cranes or excavators, can halt progress and lead to idle time for crews. Regular maintenance and timely upgrades are essential to minimize the risk of breakdowns.
The adoption of advanced technology, such as project management software, can also improve efficiency. When technology systems fail, delays can result from mismanaged timelines or overlooked tasks. Ensuring that all tools and equipment are in top condition is critical in maintaining the overall flow of construction activities.